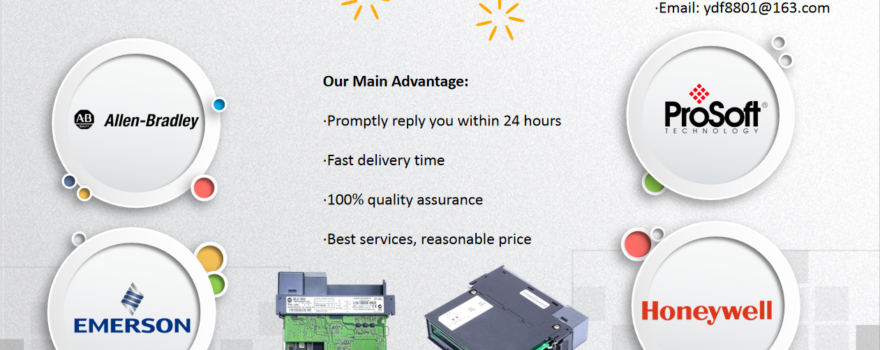
1. Used for switch quantity control
The ability of PLC to control switch quantities is very strong. The number of input and output points controlled can range from a few dozen or tens of points, to several hundred, thousands, or even tens of thousands. Due to its ability to connect to the internet, the number of points is almost unlimited, and no matter how many points are controlled, the logic problems controlled can be diverse: combination, timing, real-time, delayed, non counting, counting, fixed order, random work, and so on, all of which can be carried out.
The hardware structure of PLC is variable, and the software program is programmable, making it very flexible when used for control. If necessary, multiple sets or groups of programs can be written and called as needed. It is very suitable for the needs of multiple working conditions and state transitions in industrial sites.
There are many examples of using PLC for switch quantity control, which are needed in almost all industrial industries such as metallurgy, machinery, light industry, chemical industry, textile, etc. At present, the primary goal of PLC is incomparable to other controllers, which is that it can be conveniently and reliably used for switch quantity control.
2. Used for analog control
Analog quantities, such as current, voltage, temperature, pressure, etc., vary continuously in magnitude. Industrial production, especially continuous production processes, often requires control over these physical quantities.
As an industrial control electronic device, if PLC cannot control these quantities, it is a major drawback. Therefore, various PLC manufacturers are conducting extensive development in this area. At present, not only large and medium-sized computers can perform analog control, but even small computers can also perform such control. PLC should be equipped with A/D and D/A units for converting analog and digital signals for analog control. It is also an I/O unit, but a special I/O unit.
The A/D unit converts analog signals from external circuits into digital signals and sends them to the PLC; The D/A unit converts the digital signals of the PLC into analog signals and sends them to the external circuit. As a special type of I/O unit, it still has characteristics such as anti-interference of I/O circuits, isolation of internal and external circuits, and exchange of information with input/output relays (or internal relays, which are also an area of PLC working memory that can be read and written).
The A in A/D here mostly refers to current, voltage, and also temperature. A in D/A is mostly voltage or current. The range of voltage and current variation is mostly 0-5V, 0-10V, 4-20mA, and some can also handle positive and negative values. The D here is mostly an 8-bit binary number for small computers, and a 12 bit binary number for medium and large computers. A/D and D/A have both single and multiple channels. There are multiple input and output relays that occupy multiple channels. With A/D and D/A units, the remaining processing is all digital, which is not difficult for PLCs with information processing capabilities. Medium and large PLCs have stronger processing capabilities. They can not only add, subtract, multiply, and divide numbers, but also perform square root and interpolation. They can also perform floating-point operations, and some even have PID instructions. They can perform proportional, differential, and integral operations on deviation measures, thereby generating corresponding outputs. Computers can calculate almost everything they can. In this way, it is completely possible to achieve analog control using PLC.
PLC performs analog control, and there are units combining A/D and D/A, which can be controlled using PID or fuzzy control algorithms to achieve high control quality. The advantage of using PLC for analog control is that while analog control is being carried out, the switch quantity can also be controlled. This advantage is not possessed by other controllers, or the implementation of control is not as convenient as PLC. Of course, if the system is purely analog, using a PLC may not be as cost-effective as using a regulator.
3. Used for motion control
The actual physical quantities include not only switch quantities and analog quantities, but also motion control. The displacement of machine tool components is often expressed in numerical quantities. The effective method for motion control is NC, which is digital control technology. This is a computer-based control technology born in the United States in the 1950s. It is already very popular and well-established today. At present, the CNC rate of metal cutting machine tools in advanced countries has exceeded 40% to 80%, and some even higher. PLC is also based on computer technology and is becoming increasingly sophisticated. PLC can receive counting pulses with frequencies ranging from a few k to several tens of k hertz, which can be received in multiple ways and can also be received in multiple channels. Some PLCs also have pulse output function, and the pulse frequency can reach several tens of k. With these two functions, coupled with PLC’s data processing and computing capabilities, if equipped with corresponding sensors (such as rotary encoders) or pulse servo devices, various controls can be fully implemented according to the principle of NC. High and mid-range PLCs are also developed with NC units or motion units, which can achieve point control. The motion unit can also achieve curve interpolation and control curve motion. So, if the PLC is configured with this type of unit, it is entirely possible to use the NC method for digital quantity control. The newly developed motion unit even released a programming language for NC technology, providing convenience for better digital control using PLC.
4. Used for data collection
With the development of PLC technology, its data storage area is becoming larger and larger. For example, the data storage area (DM area) of Kewei Company’s PLC can reach 9999 words. This vast data storage area can store a large amount of data. Data collection can use a counter to accumulate and record the number of pulses collected, and periodically transfer them to the DM area. Data collection can also be done using A/D units. After converting analog signals into digital signals, they are periodically stored in the DM area. The PLC can also be configured with a small printer to regularly print out data from the DM area.
PLC can also communicate with computers, and the data in the DM area is read out by the computer and then processed by the computer. At this point, the PLC becomes the data terminal of the computer.
Power users have used PLC to record their electricity consumption in real-time, in order to achieve different charging methods for different electricity usage times and pricing, and encourage users to use more electricity during low electricity consumption periods, achieving the goal of reasonable and energy-saving electricity consumption.
5. Used for signal monitoring
There are many self-test signals and internal components in PLC, and most users have not fully utilized their functions. In fact, it can be fully used to monitor the PLC’s own work or to monitor the controlled objects. For a complex control system, especially an automatic control system, monitoring and even further self diagnosis are very necessary. It can reduce system failures, make it easy to find faults, increase the cumulative average time between failures, reduce fault repair time, and improve system reliability.
6. Used for networking and communication
PLC has strong networking and communication capabilities, and new networking structures are constantly being introduced.
PLC can be connected to personal computers for communication, and computers can participate in programming and control the management of PLC, making it more convenient to use.
In order to fully utilize the role of computers, a single computer can be used to control and manage multiple PLCs, up to 32 of which can be used. A PLC can also communicate with two or more computers to exchange information and achieve multiple monitoring of the PLC control system. PLC and PLC can also communicate, with one-on-one PLC communication and several PLCs communication, up to tens or hundreds.
PLC, intelligent instruments, and intelligent execution devices (such as frequency converters) can also be networked for communication, data exchange, and mutual operation. It can be connected into a remote control system, with a system range of up to 10 kilometers or more. It can form a local network, not only PLC, but also high-end computers and various intelligent devices can enter the network. It can be either a bus network or a ring network. The net can also be fitted with a net. Networks can also be bridged. Networking can organize thousands of PLCs, computers, and intelligent devices into one network. Nodes between networks can communicate and exchange information directly or indirectly.
Networking and communication are meeting the needs of today’s computer integrated manufacturing systems (CIMS) and the development of intelligent factories. It can enable industrial control from point to line and then to Aero, connecting equipment level control, production line control, and factory management control as a whole, thereby creating higher efficiency. This infinitely beautiful prospect has become increasingly clear in front of our generation.
The above points of application are emphasized from a qualitative perspective. In terms of quantity, PLCs come in both large and small sizes. So its control range can also be large or small. Small ones only control one device, even one component, one site; Large ones can control multiple devices, one production line, and even the entire factory. It can be said that PLC is indispensable in various occasions of industrial control.