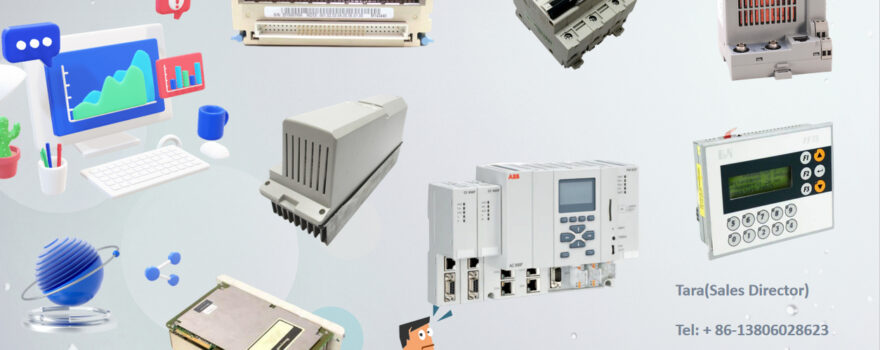
1. Material Requirements Planning
The material requirement plan provided by the MES system is fundamentally different from the material requirement plan provided by the traditional BOM-MRP method. Firstly, meet the requirements of capacity constraints, various production constraints, optimize production scheduling, and improve work efficiency. Secondly, it has detailed time information in minutes. Providing these data to ERP can greatly improve the management level of procurement and inventory modules.
Procurement module: MES accurate material requirement planning is an important basis for procurement. It is associated with the original procurement delivery time, supplier information, and price management of the procurement module, enabling enterprises to obtain more accurate and optimized procurement plans, which will directly reduce the inventory of production raw materials.
Inventory module: The detailed material requirement plan of MES can directly generate inventory in and out documents in the ERP module. The file contains detailed information such as variety, quantity, time, and plan number, greatly reducing the workload of the inventory module, improving the accuracy of inventory planning, and making inventory management more scientific and standardized.
2. Procurement arrival information
The MES system needs to extract the estimated inventory quantity of materials during the production scheduling calculation process to ensure that the supply of raw materials meets production needs.
The goal of the MES system is to develop a “future” plan, so what it requires is a future, estimated inventory quantity of materials; The ERP inventory module provides both “previous” and “current” material quantities.
In order to obtain the future inventory quantity, the MES system needs to obtain the estimated arrival quantity and time of raw materials. This information originally needs to be manually entered in the MES system, but if the user has implemented the ERP procurement module, they can obtain this data from the purchase order information.
Regarding this, MES has the function of reading ERP purchase order related information and importing future inventory into the MES system. This requires the ERP software to open data tables related to purchase orders in the database.
3. Finished product output plan
The material plan of the MES system generates both a demand plan and an output plan. The output plan of MES products has the same characteristics as the demand plan, meeting multiple constraints and being precise to the minute. Enterprises can use it to develop detailed and accurate sales and transportation plans, which is of great significance for improving the level of these modules.
4. Sales Order Information
When scheduling production, the MES system first needs information such as “When? What is produced? How much is produced?”. These pieces of information are generally stored in sales orders or main production planning modules in the ERP system. In addition to manually re entering this information in the MES system, you can also directly retrieve this information from the ERP system, process it, and directly issue production schedules to obtain specific production plans.
5. Cost plan and cost allocation data
The MES system automatically generates a production cost plan based on the production operation plan, material cost, and resource cost per unit time. The MES system can also allocate costs to various processes based on actual production execution data, and obtain the actual costs incurred. These pieces of information can be transmitted together to the finance module, which can enhance the cost management function of finance.
6. Detailed homework plan (process plan) and personnel salary, equipment management, quality management
MES generates detailed job plans or job plans, which in turn generate production resource plans. Each process contains rich information and may involve certain personnel and salary management; It may also be associated with equipment, teams, and other resources; It may also be related to quality management. With a homework plan, ERP can improve the management of these modules, and the specific functions and methods should also be linked to the needs of actual users and ERP software.